Manufacturing Process
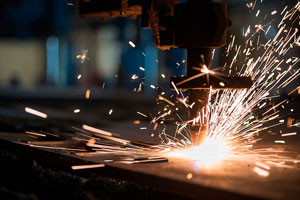
Stainless steel sheet metal is selected and cut to the size and shape required for the sink using specialized machineries such as laser cutters, shears, or saws.
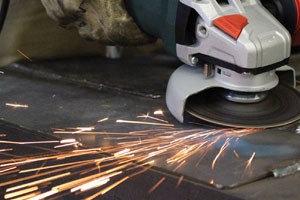
The edges of the metal are then trimmed and smoothed to remove any burrs or sharp edges. This is typically done using a grinding wheel or belt sander.
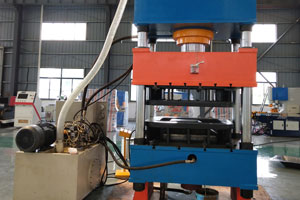
The sink bowl is formed using a hydraulic press or stamping machine. A die, which is a tool that shapes the metal, is used to press the metal into the desired shape. The press or stamping machine applies pressure to the die, which forces the metal into the shape of the sink bowl.
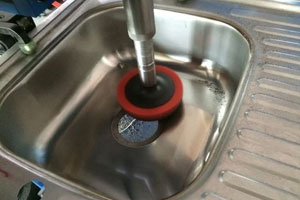
The sink is polished using a polishing wheel, which is a large wheel that spins rapidly and has an abrasive surface. The sink is held against the polishing wheel, which removes any rough edges and creates a smooth, shiny finish.
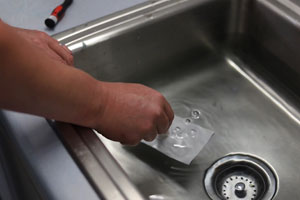
Finally, the sink undergoes quality control to ensure that it meets industry standards and is free from defects. This may involve checking for leaks, testing the sink for durability, and inspecting the sink for any imperfections or blemishes.
Manufacturing Process
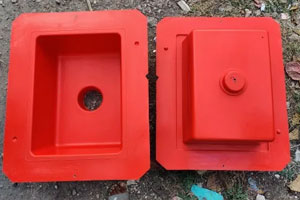
A mold is created to the size and shape of the sink. The mold is typically made from plaster, fiberglass, or silicone.
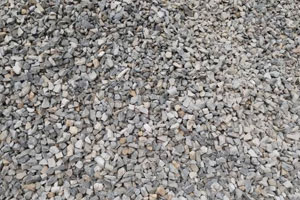
A mixture of crushed quartz, resin, and pigment is mixed together in a large container. The exact recipe may vary depending on the manufacturer, but typically, the mixture contains around 93% quartz and 7% resin and pigment.
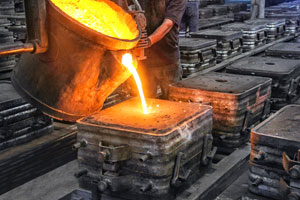
The mixed quartz composite is poured into the mold and spread evenly using a tool such as a trowel.
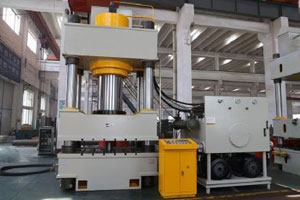
The mixture is compressed using a vacuum or hydraulic press. This helps to remove any air bubbles and ensure that the sink is uniform in density and strength.
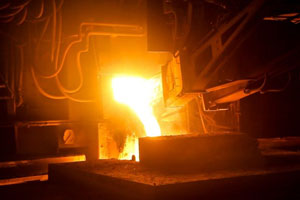
The sink is then cured in a special oven at high temperatures. The heat helps to harden the resin and create a strong, durable sink.
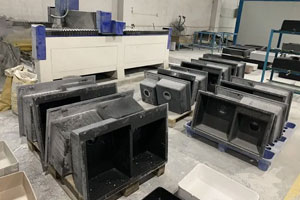
Once the sink is cured, it is removed from the mold. Any rough edges are smoothed out and the sink is cleaned.
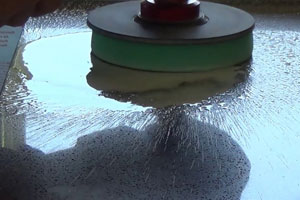
The sink is polished using a polishing wheel, which is a large wheel that spins rapidly and has an abrasive surface. The sink is held against the polishing wheel, which removes any rough edges and creates a smooth, glossy finish.
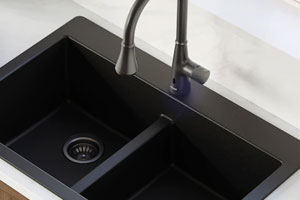
Holes for the faucet and drain are cut into the sink using specialized machinery such as a CNC router.
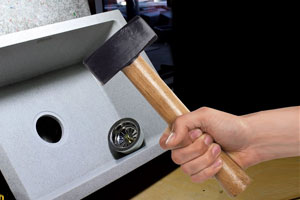
Finally, the sink undergoes quality control to ensure that it meets industry standards and is free from defects. This may involve checking for leaks, testing the sink for durability, and inspecting the sink for any imperfections or blemishes.