Manufacturing Process
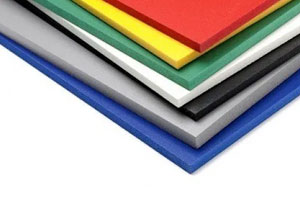
The main raw materials used in the production of PVC vanities include PVC sheets, MDF (medium-density fiberboard) panels, and hardware components such as handles and hinges. These materials are sourced from suppliers and checked for quality and consistency.
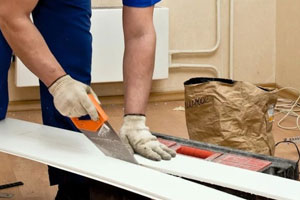
The PVC sheets and MDF panels are cut into the desired size and shape using a combination of saws, drills, and other cutting tools. The edges are then smoothed and finished to create a clean, even surface.
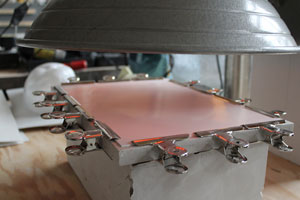
The PVC sheets are then heated and formed into the desired shape using a vacuum forming or thermoforming process. This process involves applying heat to the PVC sheets and using a mold to shape them into the desired form.
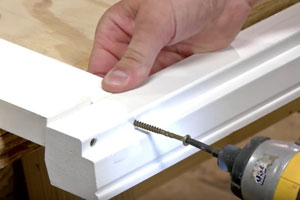
The PVC panels and MDF panels are joined and assembled to create a complete vanity. This process involves using screws, adhesives, or other fastening methods to securely attach the panels to each other and to the hardware components.
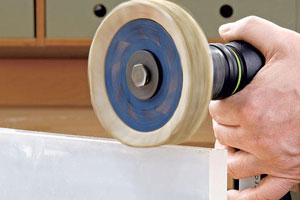
The surface of the vanity is finished using a variety of techniques to create a smooth, even surface. This may involve sanding, polishing, or painting the surface to achieve the desired finish.
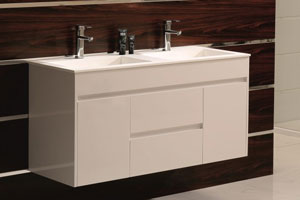
Once the PVC vanity is finished, it undergoes rigorous quality control checks to ensure that it meets industry standards for durability, appearance, and performance.
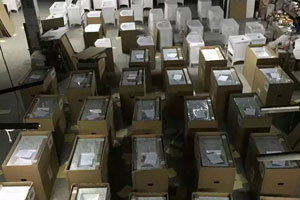
Finally, the vanity is packaged and shipped to distributors or retailers for sale.